Avoiding Networked Lighting Control System Deployment Pitfalls
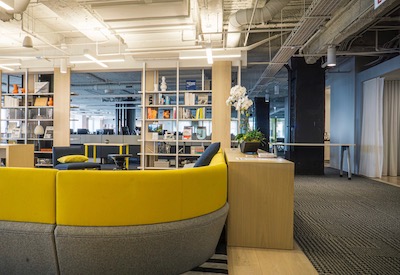
June 15, 2021
My blog post from April 1, 2020, entitled Lessons Learned from Living Lab describes a research project about retrofitting existing spaces with networked lighting control systems (NLCs). It contains recommendations on how to avoid typical of problems that may be encountered on an NLC install. This post will elaborate on some of those “lessons” and recommendations.
The discussion in the previous blog post centered around systems deployed in two of the four quadrants. Here’s a brief summary of the equipment in each.
Quadrant 1
• Individual pendant-mounted 5′ LED fixtures with separately controlled uplight vs. downlight components
• Wireless NLC with central server; controllers use 0-10V dimming protocol
• Standalone wireless sensors and switches
Quadrant 2
• Continuous 28′-long rows of pendant-mounted LED fixtures; uplight and downlight could not be separately controlled due to the fixture design
• Each row consisted of (3) 8′ segments and (1) 4′ segment, butted together to form a continuous 28′ row
• Wired NLC with central server; fixtures used DALI drivers
• Standalone wired sensors and switches (using a proprietary protocol)
As mentioned, the previous blog post did list some recommendations on how to avoid some of the issues that arose during installation. We’ll elaborate on them now, so here goes.
Quadrant 1, Issue 1
The fixture manufacturer said that they could not pre-install the controllers in the fixture housing, and therefore the electricians had to install two controllers for each fixture remotely in the plenum, bringing a total of 9 wires down two separate SJ cords.
• Ask fixture vendors for dimensioned drawings or — preferably — sample fixtures so that you can check beforehand if there is room to pre-install controls components.
• If there is room to install controls components in fixtures, and the fixture vendor doesn’t have a good reason not to, but won’t – then use a different fixture vendor.
• If there is room to pre-install controls components in fixtures – then do so. It saves a huge amount of time and vastly reduces installation complexity on-site. This will probably require that the fixture vendor buy the control components on an OEM basis from the controls vendor, so make sure you allow sufficient time for this to happen.
• Ask fixture vendors to use standard wire colours.
• Whether using standard wire colours or not, ask fixture vendors to label all wires.
Quadrant 1, Issue 2
This NLC vendor had UL924-rated controllers for EM lighting but only in wired versions. They had to be tethered to a port in a nearby wireless controller. The diagram explaining this wasn’t incredibly clear, so the electricians didn’t really know how to wire these EM-rated controllers on the first night of installation.
• Make sure vendors provide job-specific drawings for any non-standard conditions, especially if they are not shown anywhere else such as on cut sheets.
• If a controls vendor provides on-line resources such as PDFs of drawings, and/or YouTube videos (for example showing wiring for non-standard conditions) — great. However, you should still require that they print out and include such drawings with their shipment anyway.
• If a controls vendor has a system that requires third-party equipment (such as UL924 EM relays, plug-load controllers, etc.), consider using a different system that already contains those pieces of equipment — or where a UL924 listing has been obtained for what are otherwise standard devices such as controllers.
• Ask fixture and/or controls vendors to label fixtures to indicate if they need normal power or emergency power.
Quadrant 1, Issue 3
When fixtures were initially energized — and before the lighting control system was commissioned — some fixtures only came on to minimum light levels. The electrical contractor claimed that it was because of defective drivers (which wasn’t true). As a result, they insisted on getting replacement drivers, which held up the installation work. (Sidebar discussion: if you’re using 0-10V dimmable drivers and they are dimmed before commissioning of the NLC, then the likelihood is about 99.99% that they shorted the 0-10V wires.)
• Assuming it’s possible, ask the fixture vendor to pre-install controls components in fixtures. This will eliminate wiring problems because the electrician will only have to connect line-voltage power wires (black, white and green) on the job site.
• Ask the fixture vendors to test all fixtures for proper operation in the factory prior to shipment to the job site.
Quadrant 2, Issue 1
A specific type of low-voltage cable for the peripherals (sensors and switches) was not on site on the first night of installation. There was a note on the drawings that the electrical contractor needed to order that based on the total length required — in advance. This was not done! As a result, they actually opened up the ceiling tiles on three separate occasions: 1) to bring power to the fixtures; 2) to bring the low-voltage DALI wires to the fixtures; 3) to run the special low-voltage cable to the sensors and switches. Opening ceiling tiles on multiple occasions in a retrofit project is extremely problematic.
• At the outset of the project, decide who will be the point person responsible for reviewing all contract documents (such as submittal drawings), and who is also responsible for communicating to everyone else involved in the project (controls vendors, distributors, contractors, owner, etc.). This person would have been responsible for pre-ordering any special cable (or any other required hardware).
• Consider using control systems that don’t require the vendors, distributor or contractors to provide anything non-standard. For example, there are in fact DALI-compliant sensors and switches, and therefore they do not require the use of things like special cable provided by a third party.
• Alternately, consider using a system that uses wireless peripherals (sensors, switches, etc.), even if the fixtures/controllers used a wired protocol (such as DALI).
• Consider using MC cables that contain separate sets of jacketed conductors. These can provide conductors for the line-voltage (power) part of the controllers or drivers, as well as separate conductors for the low-voltage (communication or dimming) part of the controllers or drivers — whether they use 0-10V or digital (e.g., DALI) protocol. This way, all required conductors are already contained in a single MC cable.
Quadrant 2, Issue 2
Each fixture segment had its own driver (and junction box) in the plenum. However, because the fixtures were supplied as mostly 8′ segments, they couldn’t separate some of the 4′ EM segments within the normal powered (8′) segments as indicated on the drawing. This had an impact on the power supply from the emergency generators. If this had been installed throughout the entire building, the impact on load on the generator would have been huge. By the way, by code, you can’t mix drivers for “normally powered” segments and for EM segments in the same junction box.
Sidebar discussion on EM loads on the generator
In Quadrant 2, there were (10) EM segments. So, we can assume that on each floor there would be about (40) EM segments total. (40) EM segments per floor x (43) floors = (1720) total EM segments.
Drivers for 4′ segments were 29 watts. Drivers for 8′ segments were 48 watts. The incremental difference was therefore 19 watts.
THEREFORE … if EM power had been connected to the longer 8′ segments throughout the building, that would have resulted in an incremental increase of load on the EM generator of 1720 segments x 19 watts = 32,680 watts.
Moral of the story: this is a very consequential determination. This is not something to deal with casually.
• If an installation requires the contractor to figure out what goes where, the point person should make sure that precise drawings are on the job site during installation.
• Needless to say, the point person should also approve “submittal” drawings after verifying that the fixture and control vendors will be providing what the owner and/or specifier expect.
• This is particularly important in the case of fixtures mounted in linear rows comprised of individual segments, especially if they are not all the same (as is the case when some segments may be designated for EM lighting).
• The point person should also be on site at least at the start of installation to ensure that the contractor knows exactly what to install where.
• Preferably, there should be a pre-install or even pre-bid meeting to review these types of issues.
Quadrant 2, Issue 3
The controls manufacturer didn’t make LED drivers using the DALI protocol. They said that drivers made by a particular company which were based on the DALI protocol could be used instead. However, these drivers were kind of like DALI+ (because they add extra code on top of the normal DALI coding). However, it turns out that the NLC system and the drivers weren’t 100% compatible, and the fixtures didn’t dim in response to the photosensors. (Just to be clear, both the NLC from one vendor and the drivers from the other vendor are great products. Unfortunately, they are not 100% compatible.)
• Make sure that fixture and controls vendors have tested samples of all equipment prior to fabrication and can verify that they perform as required.
• Ask vendors to provide a written statement to the owner and/or specifier verifying that all equipment performs as required.
• THEREFORE, if any equipment as installed doesn’t work as required the onus will be on the vendors to remedy the problem at their expense.
Quadrant 2, Issue 4
Control devices in panels weren’t marked to indicate which wires needed to be landed where. A site visit by a factory rep was scheduled for a later date to review this and provide markings (on blue painter’s tape!) before installation could be completed. Needless to say, that delayed completion of work in this quadrant.
• Require vendors to submit drawings showing all connections/terminations that the contractor must make on-site.
• Alternatively, provide indications on the equipment itself showing all connections/terminations.
• Alternatively, require that a factory rep is on-site at least at the beginning of installation to assist the contractor in determining exactly which wires to land where.
• D.) All of the above!
This is a very comprehensive laundry list of issues that arose during a real-life NLC deployment on a retrofit project. It’s not meant to scare you or convince you that it’s hard to deploy an NLC in a retrofit (or even a new) project. It’s not. But selecting, specifying, installing, commissioning and operating any system requires you to dot “I’s” and cross “T’s”.
Are there any major summaries we can draw from these observations? Yes:
• For any NLC deployment — whether for a new or retrofit project — you absolutely must commit to dotting “I’s” and crossing “T’s”. This is really not very complicated stuff. But you cannot not commit to the minimal effort required beforehand to ensure that you will prevent easily avoidable problems.
• It’s disheartening to see how casual many people and companies are when it comes to retrofitting or deploying NLCs in new buildings. For example, if the base building fixtures are used for EM lighting (as they are in most spaces), making changes to either the fixtures or the controls (or both) will automatically impact the EM lighting. Since this is a life safety issue, someone qualified (e.g., an electrical engineer) really should be signing off on these deployments to verify that they will still provide emergency egress lighting required by code. This isn’t the most complicated thing in the world. But don’t let this be the tail that wags the dog just to find out that an inspector won’t sign off your project.
• There are a lot of really great vendors, products, salespeople and sales reps out there for NLCs. Having said that, it was remarkable how little documentation or other informational material was provided, even for a project in a 43-storey office tower in NYC. The point person you designate should make sure that he or she understands every single aspect of the equipment and how things connect, and how they work — beforehand. Do not automatically assume that any vendor will hold your hand throughout the entire process. If you have any questions at all, ask them.
• Many of the issues that arose were due to the fact that the electrical contractor had to wire controls components in the field. If you use an NLC with fixture-integrated sensors (and controllers) — typically called LLLC (luminaire level lighting controls) — then that would eliminate many of the problems that cropped up.
• Some of the issues that arose were due to the fact that the quadrant used a wired NLC. If you use a wireless NLC, that will certainly eliminate the possibility for miswiring that may occur using a wired NLC system.
Does this mean that you have to use an NLC with fixture-integrated sensors and controllers (LLLC)? And that you have to use an NLC that’s wireless? No. There are situations where a wired system may be warranted or desired; for example, because of security concerns. But if your most important goal is to prevent installation problems, then it’s a safe bet that a wireless system using LLLC (fixture-integrated sensors and controllers) is the way to go.
Hopefully, you will decide that these are very simple precautions that, if taken beforehand, can help guarantee an extremely successful deployment of a networked lighting control system.
Steve Mesh is an award-winning lighting designer who has designed lighting and control systems for a variety of project types (commercial, museums, schools, residential, restaurants, retail, historic, healthcare, etc.). As an educator, he has taught classes and given presentations about lighting and controls across North America and internationally. One of his is developing lighting and lighting controls courses that rely on hands-on and/or interactive content. He has been a repeat speaker at LightFair for many years.
Published with the permission of Lighting Controls Association.