The Engineer’s Guide to RFIs
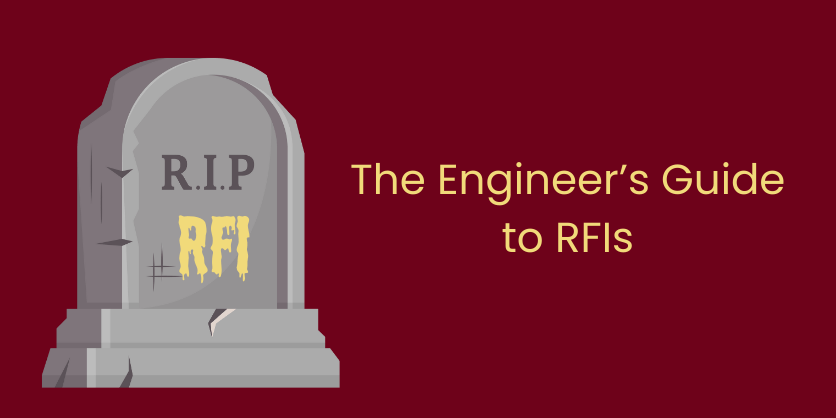
By Emily Lai, LC
What’s your idea of a successful project? For me, it’s silence — no emails, no phone calls, just the peaceful hum of a perfectly executed job. In reality, though, we all know the sinking feeling when the dreaded RFIs hit our inboxes, and we collectively wonder, “Is this going to lead to a change order?”
Yes, those little queries from electrical contractors trying to make sense of our diagrams and notes can send us into a panic! Help is here. Let’s walk through some common RFI nightmares — and how to avoid them.
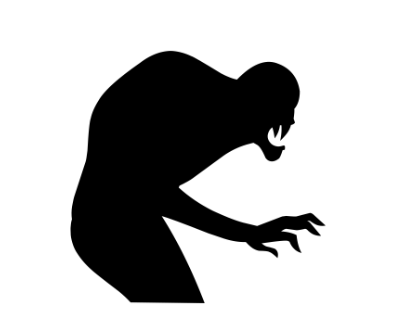
Nightmare # 1
Wiring Diagrams: The “Which Wire Goes Where?” RFI
Ever put together a LEGO™ set? Whether it’s a 50-piece build or an elaborate 5,000-piece Millennium Falcon, the instructions are clear, the parts are labeled, and the steps are laid out. Contractors need the same level of detail in your diagrams.
A good rule of thumb is to label everything. Leave even the slightest ambiguity, and you’ll get an RFI faster than you can say “line-voltage short-circuit.” Use manufacturer-specific, one-line diagrams whenever possible, and be thorough.
I once had a project where the spec was open to both wired and wireless systems. The contractor quoted a wired system, but estimated the labor cost for wireless. It wasn’t until the pre-wire meeting that they realized the discrepancy. It was not a good surprise.
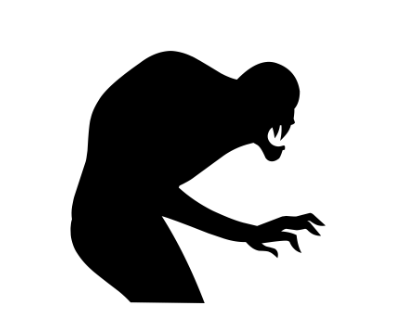
Compatibility: The “Frankenstein System” RFI
You’ve designed a beautiful system with cutting-edge controls. Everything coordinates perfectly with the light fixtures — until the contractor gets his hands on some third-party equipment. That’s when you get the RFI, “Can these DALI drivers work with the 0-10V dimming panel?” Or worse, “Can we just add a phase dimming adapter?” Or “What if we remove half of the components off the network system and make them stand-alone?”
More than once, I’ve had a contractor swap DALI fixtures for 0-10V ones. That’s not a huge deal — except they had already pre-piped for a DALI daisy chain network. This resulted in additional piping and wiring for 0-10V zoning. A simple DALI system suddenly had to be split into two systems.
The key is to communicate upfront about which components must match, and if substitutions happen (and they will), make sure they’re compatible. Otherwise, you’ll end up with a lighting system that Dr. Frankenstein would be proud of.
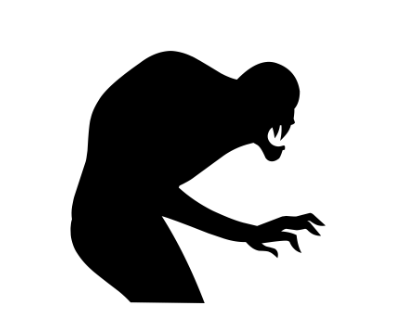
Control Strategy: The “Wait, How’s This Supposed to Work?” RFI
There’s nothing like getting an RFI late in the game that says, “Are the vacancy sensors in the hallway supposed to turn off everything? It’s making people feel like they’re in a horror movie.”
Clients might not know what they want, but they’ll definitely tell you what they don’t want when the lights suddenly go rogue.
To avoid this, write control strategies like you’re explaining them to a second grader. Remember, not everyone has a degree in lighting control. Keep it simple. Nobody wants a lighting system that requires extensive training.
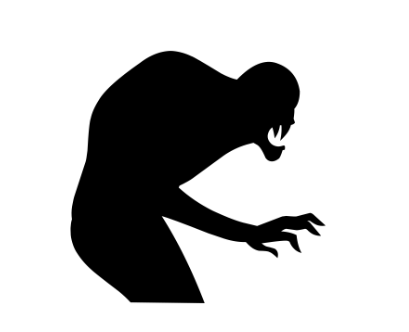
Network & Communication: The “NASA-Controlled” RFI
Enter the world of networked lighting control. Now your RFIs involve IP addresses, BACnet gateways, and contractors who feel like they’re setting up a mission to Mars. You’ll get questions like, “How many devices can we support before the system crashes?”
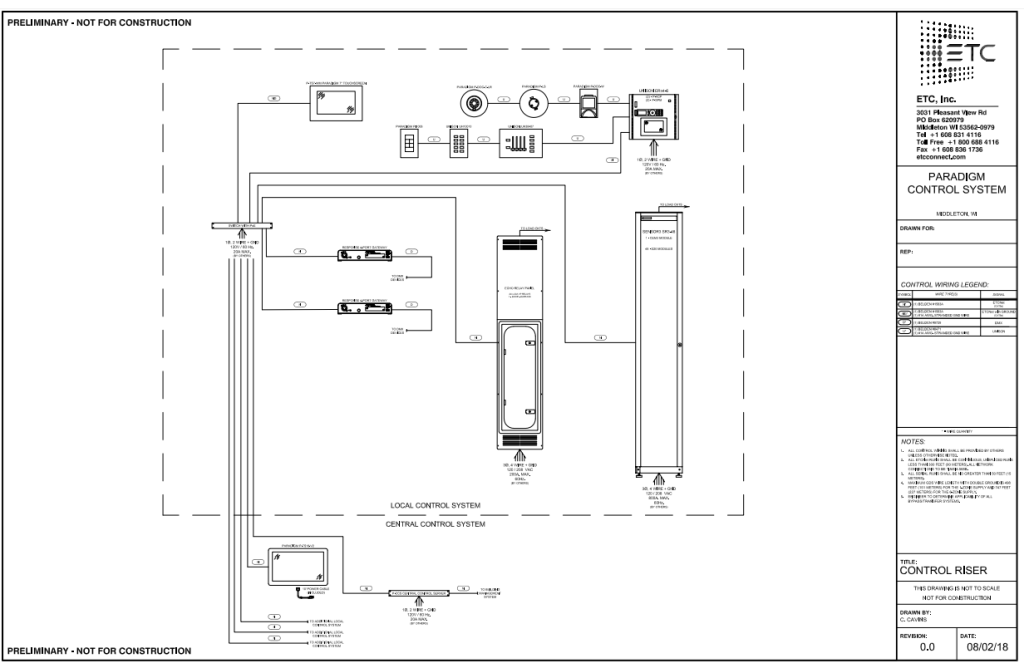
Each control system is like learning a new language — one that involves blinking lights and mysterious network failures. To avoid confusion, provide clear diagrams of the network architecture, specify gateway locations, distance limitations, and detail how many devices can connect to each gateway. The clearer you are, the fewer RFIs you’ll get, and the less likely the contractor will feel the need to call NASA for backup — or worse, call you. Get the manufacturer reps involved to help; you don’t need to know every detail of their system.
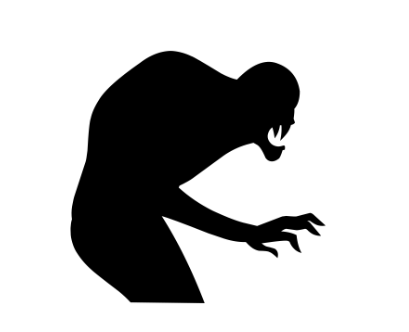
Programming & Commissioning: The “Press All the Buttons” RFI
One of my favorite RFIs was from a contractor who had finished installing everything, but had no idea how to commission the system. The email read, “Hey, we’re done, but when we press this button, the lights flicker like a disco. Any tips?”
Pro tip: Stop pressing all the buttons.
Programming and commissioning lighting systems can be tricky, especially with different zones, dimming levels, and scene settings. Clear programming instructions are a must. Define your scenes upfront — ideally before the programmer is on-site. Once they leave, it’s going to cost you to bring them back, and nobody wants to pay extra just to turn on the lights.
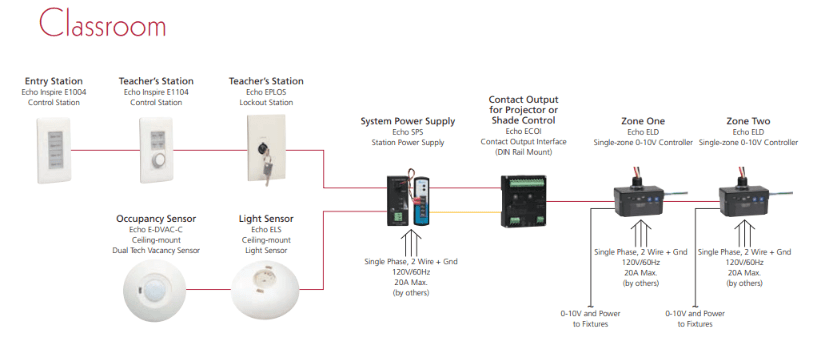
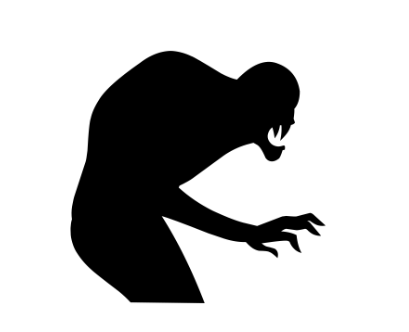
Nightmare #6
Product Substitutions: The “We Couldn’t Get What You Spec’d” RFI
Finally, we arrive at the classic product substitution RFI. The contractor sends you a message, “Hey, the system you spec’d is backordered for six weeks. Can we use this other one that looks similar?”
It might look similar, but as we know, not all systems are created equal. A quick product swap can derail an entire project if the specs don’t align perfectly. Before you approve a substitution, double-check that it will work — not just now, but in the future. Does it meet the control intent, sequence of operation, allow for future expansion, and meet the owner’s/architect’s/designer’s aesthetic? Otherwise, you’ll have clients stuck with a system that’s impossible to scale, upgrade, or even maintain.
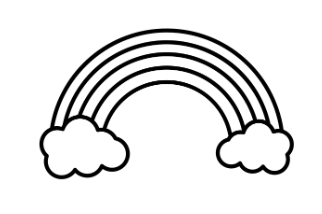
Let There Be (Less Confusing) Light
At the end of the day, RFIs are just part of life for lighting control engineers. But by providing detailed diagrams, clear programming instructions, and flexible device placement guidelines, you can minimize the “Is it supposed to do that?” questions. Keep things simple, logical, and remember: every RFI is just another opportunity to bring a little more light (pun intended) to the world.
About the Author
Emily Lai, LC, is Commercial Regional Sales Manager at ETC
Related article